The Makhmali Way: The Technical Complexities of Velvet Handloom Weaving
After witnessing years of glory, in the 19th century the intricate and time-consuming art of silk velvet weaving came up against competition from velvet powerlooms, which led to its rapid decline and near disappearance. Cholapur, Benaras, became the new home to an age-old technique of handloom velvet weaving. An intriguing drawloom, set up by Rahul Jain, textile historian, studied various historical velvet weaves including the Mughal, Ottoman and Safavid velvets to develop this loom. This particular drawloom produces a fabric which imitates the historical velvet weaves, however it cannot be said that the looms of the yesteryear had the same build since no physical evidences of those looms remain. Since there were no surviving examples of ancient velvet weaving handlooms, the fabric weave was understood and the loom design was accordingly conceptualized and subsequently established in 1993.
Shamim Ansariji, a local of Cholapur, and his family members, work on the loom to produce merely an inch of this fabric per day. Shamimji plays the role of the Master Weaver, his brothers Bilas Ansariji and Shavalay Ansariji play the role of the drawboy and helper respectively, other family members including Rizwanaji would also play the role of a helper during the process of weaving.
The complexity of handloom velvet weaving requires a strong knowledge base of weaving techniques and processes, to understand why a particular method with a particular weave is followed to produce the desired fabric.
The pattern to be woven is first conceptualized and drawn on a graph. The graph acts like a guide to understand how should the warps and wefts should be placed in order to get the desired pattern. It is then transferred onto the loom in the form of a jala naksha. The jala is essentially an attachment present at the upper end of the loom. A complex series of threads are arranged in such a manner that lifting of a particular set of threads results in the lifting of a particular set of warp yarns which results in the formation of the desired design when woven. For manipulation, the threads of the jala naksha consist of loops at the lower edge through which a set of warp yarns which are to be manipulated in a similar manner are passed. These threads are attached to a certain number of warp yarns. On raising a particular set of jala threads, the corresponding warp threads looped with it also rise, forming a shed through which the filling yarns are passed.
The jala is essentially a system of lashes and leashes which enables the weaving of highly intricate patterns on fabric (Bhandari 2014). On the one end, carefully placed and arranged, each warp yarn is wound on individual tubes known as firki, with horseshoe-shaped weights hanging at the ends to weigh down the structure and hold it in place. The warp threads then move forward through the anni which streamlines all the warp threads coming from various directions towards the weaver into the width of the fabric to be woven. To determine the threads to be lifted at a particular time during the weaving process the threads pass through the naka which are the thread loops formed according to the pattern transferred onto the loom in the form of a jala naksha.
From the naka they pass though the gulla. Gulla are the heddles through which the warp yarns are passed. For the pattern being woven in the video, 21 frames with heddles were used. The frames are referred to as kaadi. The lifting of the frames is controlled by the master weaver though pedals present under the loom. After passing through the gulla, the threads again pass through another anni, finally reaching to where the master weaver is sitting.
For the weft or the filling yarns, a shuttle is prepared which contains the thread wound on a reel. The shuttle moves horizontally between the space created by the lifted and un-lifted warp threads or the space otherwise known as the shed.
The warp threads are arranged, the weavers ready to weave and the filling yarns prepared to take on their role.
The master weaver controls the lifting of selected kaadi by means of a peddle to form a shed to pass the filling yarns though. At the command of the master weaver, the draw boy uses the mantha, which is a double toothed wooden structure with a handle, to lift the required warp threads to raise a set of selected warp yarns.
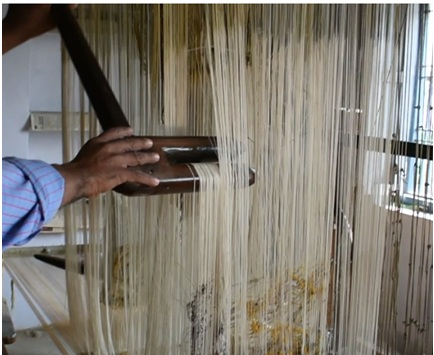
Mantha used to lift the selected jala threads
The threads lifted are kept in place using an akda, a tapering wooden instrument, present on either sides of the jala threads, till it is time to lift a different set of warp threads to continue the design being woven.
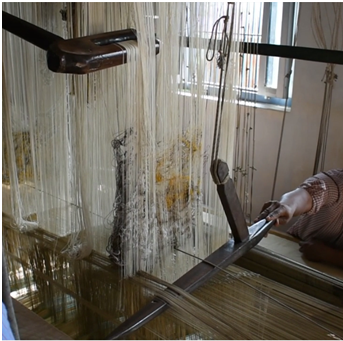
Akda holding the threads in place while the mantha lifts the jala
Before the filling yarns are passed, the lifted warp yarns have a thin metal rod placed underneath them. The thickness of the rod depends on what is the desired pile length. The higher the pile length required, the thicker will be the rod used. In the particular design being woven, the diameter of the rod was close to one soot or one millimetre.
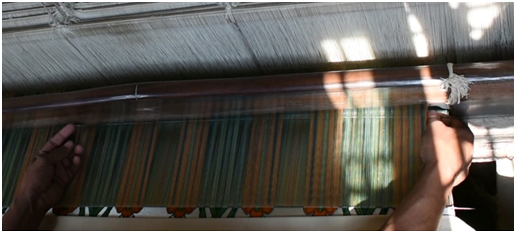
Insertion of metal rod under the warp threads for the subsequent creation of the pile
After the insertion of the metal rod, depending on the weave, filling yarns are inserted. They may be of silk, or, in this case, of zari threads.
After the weft yarn is passed, it is beaten into the fabric, with the metal rod still in place. After three to four such rods are woven in place, the pile in created by cutting the warp yarns present between two consecutive metal rods. This frees the rod, and creates tufts on the surface of the fabric.
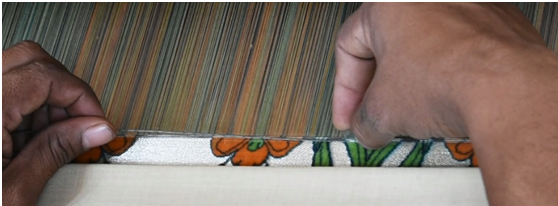
Cutting of the bound warp threads to form the pile and release the inserted metal rod
Line by line, the pattern grows, yielding only one inch of the fabric per day.
The ground weave usually used is a satin weave. A satin weave has a minimum of four wefts passing under a single warp yarn, or in other words, a single warp yarn going over a minimum of four filling yarns and then going under a filling yarn to form the weave. The role of the satin weave is to hold the warp yarns in position; else on cutting the yarns to release the rods and form the tufts, the entire system would fall apart. To ensure the unwoven yarns stay in their place, it is secured into the fabric using minimum of four weft yarns.
Patterned velvets follow a more complex weaving mechanism compared to all-over velvet fabrics, since the manipulation of threads is less. Draw looms in general follow a detailed weaving process, however, combine it with velvet and you have an art which embodies not only high levels of intricacy but a high level of creativity and understanding to plan and develop a method that involves the most compact yet elaborate form of weaving.
References
Bhandari V., 2014. Jewelled Textiles: Gold and Silver Embellished Cloth of India. Noida: Om Books International.