Mirrors have held a fascination for people since antiquity, with fine examples going back to the Old World and ancient Egypt. Decorated bronze mirrors have been amongst the most prolific of Chinese objets d’art, some being known as ‘magic mirrors’. Some of the earliest copper-base mirrors have been found from the Indian subcontinent at the Harappan site of Dholavira (c. 2500 BCE). The darpanika or maiden elegantly gazing into a mirror is a frequent theme in Indian sculptural art over the ages. Whereas metal mirror-making practices seem to have died out elsewhere in the world, a remarkable crafts survival, which was zealously guarded by hereditary families, is still prevalent in Kerala in southern India. The verdant village of Aranmula is home to an exotic traditional craft of making handcrafted, handheld metal mirrors known as val kannadi.
Aranmula, located by the meandering Pampa River, is best known for the spectacular snake-boat races which are held at the time of Onam, the most prominent Malayali religious festival. Here, a unique mirror-making tradition has thrived for centuries as a result of it being one of the items associated with wedding rituals. The wedding trousseau of brides of the Nambuthri Brahmins and the Nairs, the matrilineal warrior clan, included the ashtamangalyam of eight auspicious articles.
The reflective properties of the Aranmula mirror are astonishing and, in some ways, even better than modern-day glass mirrors. Modern glass mirrors consist of a thin sheet of glass over a reflective mercury layer. These do not give a point image due to refraction through glass. On the other hand, if one were to place the point of a pen against the Aranmula mirror, it would give a perfect point image, and with brilliant true colours as well.
How was such a highly specular polish achieved using traditional artefacts and simple handcraft alone? The author, as part of her archaeometallurgical researches, had first visited Aranmula in 1990 to explore the mirror-making craft and, subsequently, has written research papers based on studies made on samples collected from the workshops of late Gopalakrishna Achary and late Janardhan Achary.[1] These metallographic studies confirmed that the highly reflective properties of was the result of the skilful casting, optimisation and polishing of a specific highly specular bronze alloy composition. (Fig. 1)
It was found that the Aranmula metal mirrors were ingeniously made of a binary copper-tin alloy (of 32–33 per cent tin alloyed to copper), optimising the presence of the delta intermetallic compound phase of bronze of 32.6 per cent tin that forms predominantly within this narrow composition range. This silvery-white phase, due to its high reflectivity across the spectrum, is responsible for the mirror effect. It also makes for a better metal for a mirror than silver, which though it has high reflectance is very soft and dents easily, thus giving a distorted image. The delta bronze alloy, on the other hand, is very hard, even harder than steel as found by the author, and hence it can take a high polish without distortion, giving a good mirror image. However, the as-cast alloy of delta bronze (as the author has described this alloy of 32–33% tin-bronze) is very breakable. This brittleness, however, is overcome in clever ways. For one, a very thin blank was cast, of no more than a couple of millimetres, in a specially devised closed crucible-cum-mould. This is achieved by first making a two-piece mould of two clay discs, finely ground with a slip applied to get the smoothest finish. These are separated with fine spacers of the same alloy and then covered with clay such that a neck with a hollow cup is shaped. The alloy to be cast is placed in the cup, and the entire crucible-cum-mould is sealed with clay. It is then heated in a hearth with the crucible cup facing downwards.
Once the metal in the cup melts, it is tipped over so that it flows into the gap left for the mirror blank. The as-cast blank is then retrieved by breaking open the crucible-cum-mould. The silvery oval blank is then pressed onto a wooden mount with heated resin and then polished over several days to get the brilliant reflective surface. Interestingly, when one looks at sculptural depictions from Indian antiquity, such as the thirteenth-century Hoysala sculpture of the madanika (or maiden forming the strut), the mirror she holds could well represent such a mirror blank set in a wooden polishing mount. (Fig. 2) These days, however, the blank is mounted within a brass handle with a tang to be held in the hand.
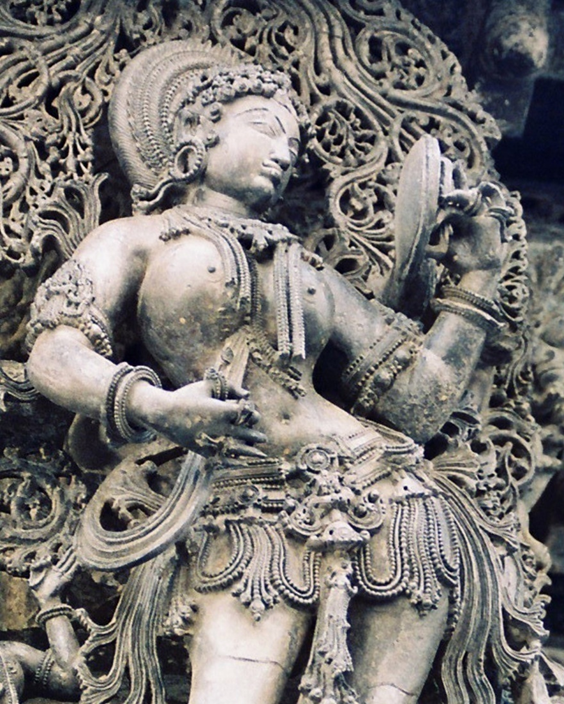
Of the local legends associated with the Aranmula mirror, one version reported by the author was that the craftspeople migrated from Sankarankoil in Tamil Nadu (with kannadi being the Tamil word for mirror as well). A widow, Parvati Ammal, is said to have dreamt up the shining alloy, which pleased the Raja of Aranmula. The spectacularly carved wooden tiered-roofed Aranmula Parthasarathy Temple is dedicated to the presiding deity Lord Krishna and overlooks the Pampa River. The alluvial clays from the banks of the Pampa provided the moulding materials for the traditional crafts for centuries. A traditional Aranmula delta bronze mirror with the seal of Travancore royalty could be technically finger-printed by the author to the seventeenth–eighteenth century through compositional and trace element analysis.[2] An example of a metal mirror was noted by the author at the Jaipur Palace Museum as well. Although further studies are needed to explore the antiquity, analysed copper-alloy mirrors from around the world or the Indian subcontinent have usually been of a lower tin content or with lead added. However, it is intriguing that a mirror uncovered by Breeks in the nineteenth century from the Nilgiri Iron Age cairns was found to be of 30 per cent tin bronze, not dissimilar to the specular bronze. Eventually, in the later medieval period, glass mirrors came into vogue through colonial influence in places such as Goa. These were of Belgian glass laid over a reflective layer of silver, often set within an almira or cupboard, although the silver has tended to tarnish over time.
The Aranmula mirror thus represents an interesting and distinctive time capsule of the history of technology of Indian and Asian antiquity. The 40-minute documentary film ‘Metal Mirror Marvel of Aranmula’, has been filmed in the workshop of master craftsman Gopukumar Achary (Fig. 3), narrated, researched, scripted and directed by the author, Sharada Srinivasan, and filmed and edited by Bala Murugesan T, in 2008.
Notes
[1] Srinivasan and Glover, ‘Wrought and quenched and cast high-tin bronzes from Kerala state’; Srinivasan and Glover, ‘Skilled mirror craft of intermetallic delta high-tin bronze (Cu31Sn8, 32.6% tin) from Aranmula, Kerala’; Srinivasan, ‘Mirrors: Metal mirrors from India.’.
[2] Srinivasan, ‘Art and Technology of south Indian and Chola bronzes,’.
Bibliography
Srinivasan, S. ‘Art and Technology of south Indian and Chola bronzes.’ Archaeology and Heritage, IIC Lectures. 2021. https://www.youtube.com/watch?v=53gLYHOAvrI
Srinivasan, S., and I. Glover. ‘Skilled mirror craft of intermetallic delta high-tin bronze (Cu31Sn8, 32.6% tin) from Aranmula, Kerala.’ Current Science 93(1): 35–40.
Srinivasan, S., and I. Glover. ‘Wrought and quenched and cast high-tin bronzes from Kerala state, southern India. Part II. Scientific investigations.’ Journal of the Historical Metallurgy Society 29(2): 75–81.
Srinivasan, S. ‘Mirrors: Metal mirrors from India.’ In Encyclopedia of the History of Science, Technology and Medicine in Non-Western Cultures, Vol. 2., edited by H. Selin, 1699-704. Berlin: Springer Verlag, 2008.
Srinivasan, S., and G. Glover. ‘Archaeometallurgical implications of new findings of traditional crafts of making high-tin ‘delta’ bronze mirrors and ‘beta’ bronze vessels in Kerala state of South India.’ In Materials Issues in Art and Archaeology V, MRS Symposium Proceedings Vol. 462, edited by P. Vandivar, J. Druzik, J. Merkel, and J. Stewart, 81–105. Warrendale: Materials Research Society, 1997.
Srinivasan, S., and I. Glover. ‘High-tin bronze mirrors of Kerala, South India.’ IAMS Newsletter, 20: 15–7.