It was long held that before the 18th century, science and technology in India lacked sophistication and was incapable of adopting any innovation. Many factors such as climate, geography, caste, despotism, anarchy were held responsible for India’s lag in technological progress, particularly when in comparison with Europe’s tempestuous advancement. These long-held and widespread assumptions notwithstanding, there were many crafts where technological change, synthesis and innovation are clearly seen (Habib n.d.:1–2). Individual fields of Indian technology such as textiles, paper and ship-building have been studied. However, there are many aspects of Indian technology that have still not received detailed investigation. A major area has been perfume technology, a large field of applied science, and a unique combination of art and science.
The technical science of Indian cosmetics and perfumery developed by ancient and medieval authors, has been reconstructed in the light of modern scientific research. Materials for such a history are found in abundance in Sanskrit, Prakrit and various other literary texts (epics such as the Ramayana, the Mahabharata and the Puranas). Textual evidence about these sciences and arts is available in the form of summaries of their contents incorporated in Sanskrit works of the encyclopaedic type such as the Brihatsamhita of Varahamihira (500 CE), the Manasollasa of King Somesvara (1130) and the Agnipurana. The earliest Sanskrit text which offers rich material related to the scientific manufacture of perfumed articles is the Brihatsamhita of Varahamihira. Different types of perfumed articles, their sources, methods of preparation, etc., have been treated in this text under the heading Gandhayukti, a term which stands for the art and science of cosmetics and perfumery. The Kamasutra of Vatsyayana also mentions the art of preparing cosmetics and perfumes as one of the 64 arts in which gentlemen of the period were expected to be proficient. Kautilya’s Arthashastra also mentions the trade of high-priced fragrant wood such as candana and its varieties, and agaru (resin of aloe) and its varieties. He also mentions that perfumed oils were made from tailaparnika trees whose wood provided essential oils; this perfume had a lasting smell, no matter whether it was made into a paste, or boiled or burnt (Krishnamurthy 1987a:72). The Sanskrit treatises on perfumery—Gandhasara of Gangadhara (between 1000 and 1600) and the Gandhavada with Marathi commentary (between 1350 and 1550), provide a good basis for the study of widespread manufacture and use of perfumes and cosmetics in India and the Indian knowledge of the same prevailing between 1200 and 1600 CE. The credit for major research in the field of perfumery and cosmetics goes to the credit of Dr Parashuram K. Gode (Labh 2000:21).
Different kinds of perfumed products and their methods of preparation are elaborated in the above-mentioned texts. On the basis of this, it has been claimed that perfumery had developed as a science in ancient India, and that our country has contributed no less to this branch of science which has now reached a very advanced stage (Krishnamurthy 1987b:72). 'Smell is fundamental to the human senses; the adaptation of the olfactory sense and that of the experiences of good and unique smells into perfumes, are a matter of technological engagement. And in this regard, the Mughal period in India was no exception. A dynamic and syncretic Indo-Muslim perfumery culture (Arnold 2004:4) evolved through continuous interaction between the twin sources of knowledge: the ancient knowledge of science and technology and the Islamic tradition.
In Mughal India, one famous discovery was that of itr-i-Jahangiri, ascribed to Nur Jahan’s mother. It was the essence obtained from distilled rose-water. Habib also subscribes to the view that the art of distillation in India, particularly that of liquor, was not brought to India by the Portuguese in the 16th century. It had been a much earlier practice and in all probability, the advanced art of distillation had rapidly travelled to India from Italy through the Islamic world. It had reached India by the 13th century and by the Mughal period, the technique had been well established (Habib 1980:23–26).
Nose, the seat of olfactory senses, was also not forgotten and to enliven it human beings invented varieties of perfumes by blending natural and synthetic substances. This was not an easy task because while the other organs could be delighted with concrete and tangible things, man had to put efforts to invent methods to extract the subtle odoriferous elements from natural sources such as roots, flowers, etc. He had then to present them through a concrete medium or vehicle, so that the enchanting odour could be retained and enjoyed for a longer period of time. This necessitated the practice of perfumery as an art as well as a science because the work of a perfume-maker consisted of a proper blending of odoriferous substances; this required artistic sensitivity as well as scientific knowledge. (Krishnamurthy 1987:71)
The term ‘perfume’ derives from incense used in the Egyptian temple (perfumare is to fill with smoke). But a perfume may be defined as any mixture of pleasantly odorous substances, incorporated in a suitable vehicle. India has been an old home to a rich perfume culture which has thrived and evolved through centuries. James McHugh points out the rich presence of a perfume culture in ancient India, deemed valuable in Sanskrit texts and that thrived in the Sanskrit courtly traditions. However, it was displaced by ‘Islamicate’ and ‘Persianate’ perfume culture and practices (which were themselves inflected by the Indian perfume culture) and ultimately by European or Western perfume culture (McHugh 2012a:117).
In medieval India, particularly Mughal India, perfume technology was a ‘creative synthesis’ (Arnold 2004:4) of the already prevailing and Islamic traditions, brought about by the process of mutual borrowing and enrichment. Far from being in cultural or technological isolation, perfumery culture in Mughal India was one of great experiments, borrowings and synthesis. Perfumery attracted considerable royal attention and investment; it was open to modifications and adaptations. It also stood as a testimony to the Mughal contribution to India’s scientific tradition resulting in a dynamic Indo-Islamic perfumery culture. The perfumery culture enjoyed a continuing vitality and fruitful intermingling of scientific traditions well into the 18th century and in all probability afterwards also. For, although from the early 16th century the Mughal court was a vital source of patronage for science and technology, the decline of its power in the 18th century did not entirely plunge the sciences into obscurity, even if the production of manuscripts produced in Sanskrit, Persian and Arabic on scientific and technical subjects showed signs of slowing down. A positive interest in science (and, increasingly, in reconciling the sciences of East and West) flourished under royal patronage in the regional courts of India: there were numerous developments, from the astronomical observatories built by Raja Jai Singh between 1722 and 1739 at Jaipur, Delhi, Mathura, Ujjain and Benares, to the eclectic medical interests and library of Indian and Western medical texts assembled by Serfoji, the last Maratha ruler of Tanjore. New centres of learning sprang up; the ones in Hyderabad under its Nizams, or in Lucknow, under the Nawabs of Awadh, specialising in Islamic science and Unani medicine, while other older, mainly Hindu, seats of learning such as Benares and Nadia in Bengal continued to flourish. Despite the withering away of Mughal power, Delhi remained a significant locus for science, art and literature, and, until the cataclysmic events of 1857, enjoyed a twilight ‘renaissance’ (McHugh 2012b:6). This, to some extent, explains the persistence of the traditional perfume technology in India till date, which has not given way completely to the western forces and present-day market competition.
Thus, the technological journey of perfumery in India has been a story of innovation, borrowing, assimilation, modifications and primarily of continuity and preservation. The beauty of this technology remains in its survival since the ancient period through centuries of modifications and preservation, till date. With such a rich technology as its backbone, perfumes during this time had great utilitarian and aesthetic value, both as an item of consumption and as a ‘commodity’.
The current ITR technology in India is locked in the fight between tradition and modernity, and this battle has extended to small businesses. The competition between Pragati Aroma Oil distillery and global groups such as Armani and Chanel mirror thousands of other battles across India between ancient practices and the forces of modernity. The makers of attar (a kind of Indian perfume) in Kannauj claim that attar making is a painstaking craft: it takes a passion for smell, love for the art, acumen and years of experience, and a special instinct derived from all these to produce the perfect attar and the delightful fragrance out of the ingredients. When talking to the few attar-producers of Kannauj who have lived there and invested in the technology for the last three to four generations, we find that all agree upon the dexterity and finesse of this art. They want to adhere to the traditional deg and bhapka system and are against the replacement of this traditional technology with new and modern machines. They believe that no machine can produce the smell of attar that experienced hands can. What music is to the musicians, word is to the poets, colour is to the painters, attar is to the attar makers in Kannauj—attar is their lifeline.
Each morning, local farmers near Kannauj pluck bagfuls of rose, jasmine and other petals and deliver them to the nearby perfume distilleries dotting this sleepy town. In a process that can take days to complete, the flowers are mixed with water and heated in copper pots. The aromatic steam is then transferred via a bamboo pipe to a receptacle containing sandalwood oil; the latter acts as the base for the attar. Moreover, the attar industry is widespread all over India, thriving in major cities such as Lucknow, Benaras, Delhi, Kolkata,and Mumbai, each of these cities having developed its own indigenous and unique perfumery culture and industry.
While it is still popular with natural-fragrance enthusiasts, attar is increasingly shunned by India’s brand-conscious consumers, who have become used to foreign products since economic reforms in the 1990s opened up the country's markets. Rising raw material costs, particularly of oil which must be imported because of limited production in India, and the rising cost of sandalwood oil and ban on the cutting of the sandalwood tree (the oil of which formed the base of attar) are major reasons for the ostracization of this perfume. The city of Kannauj boasted nearly 700 distilleries up until the late 1990s which have now reduced to some 150—200 distilleries (Srivastava 2012). However, certain initiatives have been undertaken to preserve the traditional technology of perfume making in India and boost the attar industry through the foundation of the Fragrance & Flavour Development Centre (FFDC) at Kannauj in the year 1991 by the Government of India with the assistance of UNDP/UNIDO and the Government of Uttar Pradesh. FFDC aims to serve as an interface between the essential oil, fragrance and flavour industry and the R & D institutions both in the field of agro and chemical technology. The main objective of the centre is to serve, sustain and upgrade the status of farmers and industries engaged in aromatic cultivation and processing, so as to make them competitive in both local and global markets (FFDC website). Also, R & D support for the cultivation of aromatic plants is generated through the Central Institute of Medicinal and Aromatic Plants, popularly known as CIMAP with its headquarters at Lucknow (CIMPAP). In 2014, on April 26, the Intellectual Property Rights Day, Kannauj perfume, one of the 14 items unique to various locations in the country, was awarded the Geographical Indications (GI) tag (Subramani 2014). Moreover, the former Uttar Pradesh Government led by Samajwadi Party’s Akhilesh Yadav came up with a visionary plan in the year 2015 of a possible ‘Kannauj-Grasse pact’, a mutual agreement between the two towns famous for their perfumes and itr (attar), respectively, and for giving Kannauj's traditional business a leg up. The pact, which is expected to facilitate technology exchange, ingredient sourcing and partnership among perfume manufacturers of the two cities, is also expected to revive and modernise the struggling indigenous perfume industry and give it international presence (Times of India 2015). However, during my field visit to Kannauj, the local people and the FFDC Director, Shakti Vinay Shukla, were not too hopeful about the implementation of the plans owing to internal feuds going on within the party: the final blow came with the defeat of the Samajwadi Party during the 2017 Uttar Pradesh elections. No fresh plans have been announced yet for the attar industry in India and for the preservation of its technology by the new government.
The centuries-old itr is the most tangible manifestation of intangible cultural heritage. It is our responsibility to safeguard and protect the craft along with the skills and knowledge of the artisans attached to it (Tabassum et.al. 2016a:71). Itr making is a labour-intensive process, requiring a combination of great talent, skill and patience (Tabassum et.al. 2016b:71), in addition to experience and passion. Unfortunately, because of the high cost of raw material and the labour-intensive nature of traditional itr making, this art is declining. It may soon be extinct if measures or steps to safeguard it are not taken up in time. It is up to us, the consumers of attar, to support the few remaining attar makers in maintaining the natural character of attar culture and tradition. However, despite being locked in the conflict of tradition versus modernity, the traditional deg and bhapka technology for attar production still manages to survive, owing to the unique patterns of its consumption continuing in the country. They survive either in the form of non-alcoholic, natural perfumes with unique qualities and a touch of human craftsmanship (particularly in cities such as Lucknow), or largely in collaboration with flavouring industries such as the paan and tobacco industries (particularly in cities such as Benaras).
It is not possible to stitch a single narrative of the continuous and living tradition of perfume-making technology in India. It has evolved, adopted, modified and survived both in form of a knowledge-system embedded in textual sources, as well as in practice. It claimed importance as a royal and refined technology, and had a vibrant presence in royal lifestyles and significant implications during the medieval period in India, especially during the Mughal period. The technology of perfume making evolved as a unique combination of art and science: it was all about finesse, minute detailing, timing, skill, knowledge of mixing the ingredients in the right proportion and pasting. However, the technology varied with each perfume, its form, its strength and its utility. For example, the technology for making a paste-powdered perfume such as bakkha varied from that of a distilled perfume such as chuva which again varied from the paste form of abir. Moreover, the methods differed according to the application on different parts of the body, different settings for use, and also with the strength of the perfume.
The culture of itr production is the heritage of the people of Kannauj; the latter has been known for natural itr from the Mughal period or even earlier. The beginning of natural itr in India which developed and progressed in and around Kannauj, is quite strong even now. The perfumeries in Kannauj still use the age-old methods to produce all natural scents to maintain the perfume’s originality and quality (Srivastava 2012). A perfumer at Pragati Aroma Distillery says, ‘It is difficult to move to the modern perfume-making technology because we do not want to let go our years of attachment to the traditional itr making technology. Our souls are connected to the process and the end product. It is natural, alcohol free, has a deep impact on mind and body. We are very much attached to it and we want to preserve it’ (interview conducted in Kannauj on December 1, 2016). Located on the banks of the river Ganges, the city boasts as being the ‘traditional perfumery capital in India’ whose glory reached its peak during the seventh century CE. What Grasse is to France, Kannauj is to India. It hosts the medieval technology of liquid perfume (itr) making through the process of steam distillation. The living tradition of techniques of steam distillation that still continue in the city of Kannauj which houses around 150-200 distillation units at present, helps us to understand the technological continuities and shifting patterns in perfume-making practices in India. It also indicates how traditional craftsmanship has survived in this country as a valuable cultural heritage.
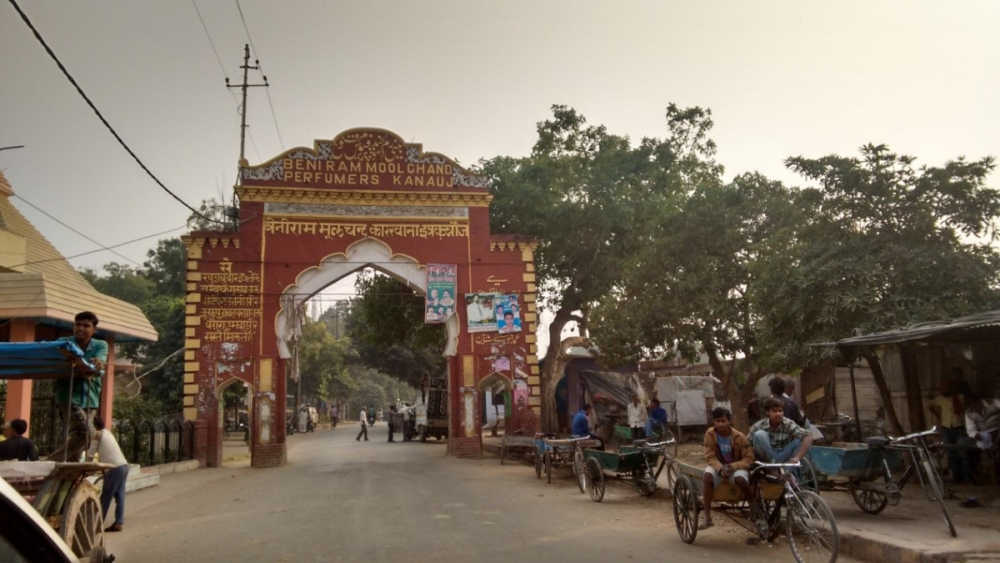
Image 1.: The main heartland of the city of Kannauj (Photograph: Amrita Chattopadhyay)
The distillation technology carried out for natural, oil-based, alcohol-free, liquid perfume (particularly itr) making at Kannauj is steam distillation or hydro-distillation. Locally called the deg and bhapka system (Kannauj)[19] the manufacturing process is as follows
The itr is manufactured traditionally through the deg and bhapka system, which is a steam distillation process. The still is heated from below by lighting a fire with the help of wood or cow dung. The temperature and speed of the distillation is controlled by regulating the fire. The distillation is managed by highly skilled/experienced workers called dighaa. He knows when the correct quantity of vapour have condensed inside the receiver by feeling the round part of the receiver under water. The water in the tank is changed continuously to prevent the temperature from rising too high. Managing the still is a highly skilled job, as the operator must keep the boiling in the still at a level that matches the condensation in the receiver, in order to keep the pressure under control. When the desired quantity of vapours has condensed, the dighaa rubs a wet cloth around the body of the still for a temporary pause in distillation and the filled receiver is replaced by another receiver. If necessary, the second may be replaced by a third receiver. The receiver is then allowed to cool and may remain idle for one or two days depending on the pressure of work. The mixture of oil and water is then separated either directly from the receiver through a hole at the bottom or pouring the whole mixture in an open trough. After the oil and water have separated into two layers, the water is removed from an opening in the bottom, and the same is cohobated. The base material (sandalwood oil) remains in the receiver. After the desired concentration of the attar has been reached, the same is poured into leather bottles for sedimentation and removal of moisture. Sometimes liquid paraffin is used for the manufacture of the cheaper attars. The mouth of the receiver is sealed by wrapping coarse cloth around the bamboo pipe and it is then pushed inside the condenser. The receiver may contain up to 5-10 kilos of base material and is kept in a small water tank. (website of Govt. of Kannauj)
In a review article, Powar et al. (2013:184) explain how the itr manufacturing of the floral type takes place in remote places because flowers must be processed quickly after plucking. Given that 'the apparatus and equipment used for manufacture of attar are light, flexible, easy to repair, and have a fair degree of efficiency', the traditional deg and bhapka is followed even now. The process follows steam distillation where there is no separate condenser and the receiver placed in water acts as the condenser.
Deg and bhapka distillation technology in Kannauj
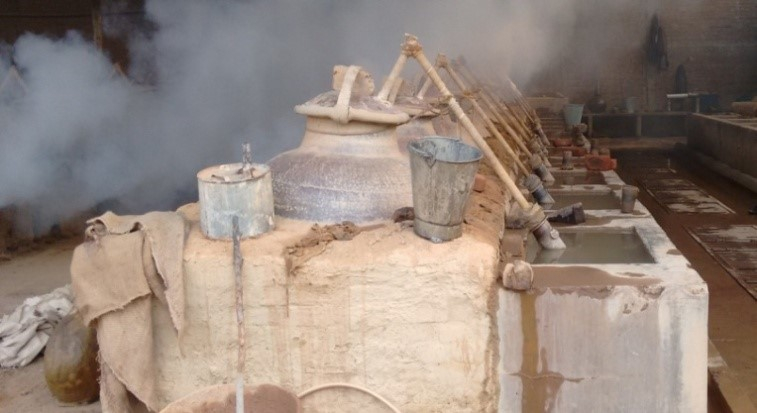
Image 2: The current deg and bhapka method practised in Kannauj (Photograph Amrita Chattopadhyay)
The website 'Indian Attars' gives details of equipment:
Deg: These are copper stills which are directly heated by fire, with capacities ranging from 10-160 kilos of floral/herbal materials. The lid (sarpos) has openings for connection to one or two receivers.
Bhapka: In attar distillation, no separate condenser is used: the unique odour is obtained by condensing vapours into the base material, mainly sandalwood oil. The receiver is built of copper, and is round with a long neck, for connection with the deg via chonga.
Chonga: Condenser made of bamboo that connects the still and receiver; it is a hollow pipe wrapped with twine for insulation.
Bhatti: Furnace, usually heated with wood or coal; the heat is controlled manually.
Gachchi: The cooling water tank where the bhapka is kept to cool the distillate from the deg.
Kuppi: Leather bottles whose semi-permeability to water allows the water to move out and the attar to remain.
Raw Materials
The website, 'Lalji Aromatic' gives a summary of raw materials and their sources: The base material is sandalwood oil, di-octylphthalate (DOP) and liquid paraffin; flowers used are gulab (rose), kewra, bela (jasmine), mehndi (henna), kadam, chameli, genda (marigold), saffron and maulshri; herbs and spices include oakmoss, sugandh mantri, laurel berry, juniper berry, cypriol, Indian valerian, jatamansi, hedychium spicatum, daru haldi, sugandha bala, sugandha kokila, kulanjan, javitri/ jaiphal, cardamom, clove, saffron, ambergris and musk.
Perfume has been adaptive to the various political changeovers, socio-economic developments and consequent technological innovations. The diverse perfume-making formulas and techniques that were researched, formulated and written down have survived till date in treatise forms or in forms of practice, comprise a huge corpus of knowledge. However, with the influence of westernization over Indian society, the advent of supreme mechanization of technology and the rise of consumerism, the current economic scenario has dramatically altered the perfume industry, its market and particularly the technology in India. Complex machines, artificial laboratory-made chemicals and huge engine-run distillation plants have taken over the current perfume technology. But as tradition always survives in some form or the other, the old traditional perfume technology has also survived in India in the form of a surviving itr industry with the city of Kannauj as its epicentre. The 5,000 year-old perfumery culture still continues to prevail and thrive in the old city of Kannauj in Uttar Pradesh.
References
Arnold, David. 2004. The New Cambridge History of India: Science, Technology and Medicine in Colonial India, vol. 3, part 5. Cambridge: Cambridge University Press.
Habib, Irfan. 1980. ‘The Technology and Economy of Mughal India', The Indian Economic and Social History Review 17.1:1–34.
Krishnamurthy, Radha. 1987. ‘Perfumery In Ancient India,’ Indian Journal of History of Science 22.1:71–79.
Labh, Vijay Lakshmi. 2000. ‘The Science of Perfumery and Cosmetics Products in Northern and Central India During Early Medieval Period (A.D.1100–1526)', in Journal of the Asiatic Society 45.1:21.
McHugh, James. 2012. Sandalwood and Carrion: Smell in Indian Religion and Culture. New York: Oxford University Press.
Powar, P.V., A.N. Lomkhade, R.B. Ambikar, P.H. Sharma, N.S. Vyawahare. 2013. ‘Aromatherapy: The Essence Science for Social Health Status’, Asian Journal of Phytomedicine and Clinical Research 1.3:180–94. Online at http://www.ajpcrjournal.com/article/POWER.pdf (viewed on April 27, 2018).
Srivastava, Abhay. 2012. 'Life: India’s perfume capital threatened by scent of modernity', Taipei Times, September 20. Online at http://www.taipeitimes.com/News/feat/archives/2012/09/20/2003543194/1 (viewed on June 21, 2017).
Subramani, A. 2014. 'Geographical Indications tag for Nagpur orange, Kannauj perfume', Times of India, April 26. Online at http://timesofindia.indiatimes.com/city/chennai/Geographical-Indications-tag-for-Nagpur-orange-Kannauj-perfume/articleshow/34214019.cms (viewed on June 21, 2017).
Tabassum, Saba, S. Asif and A. Naqvi. 2016. ‘Traditional Method of Making Attar in Kannauj’, In International Journal of Interdisciplinary Research in Science Society and Culture (IJIRSSC) 2.1:71.
Times of India. 2015. 'Scent of Success: Kannauj-Grasse pact to give leg up to "Itr" industry', Times of India, May 26. Online at http://timesofindia.indiatimes.com/city/lucknow/Scent-of-Success-Kannauj-Grasse-pact-to-give-leg-up-to-Itr-industry/articleshow/47423112.cms (viewed on June 23, 2017).
Websites
CIMAP. CSIR-Central Institute of Medicinal and Aromatic Plants. Online at http://www.cimap.res.in/english/index.php/about-us/history (viewed on June 21, 2017).
FFDC. Fragrance and Flavour Development Centre, Kannauj. Online at http://www.ffdcindia.org/default.asp (viewed on June 21, 2017).
Indian Attars. Online at http://www.indianattars.com/history_of_kannauj.html? (viewed on June 21, 2017).
Govt. of Kannauj. Online at http://kannauj.nic.in/attar.htm (viewed on June 20, 2017).
Lalji Aromatic. http://www.laljiaromatic.com/facts.htm?.