Patnulu (pronounced pātnūlu), the handspun khadi of Ponduru is one of the best surviving examples of the glorious heritage of fine-count cotton hand spinning and weaving in India. In and around the Ponduru town of Srikakulam district of Andhra Pradesh, rural women are still engaged in spinning fine-count cotton yarn, starting from the pre-spinning processes of ginning and carding, in their humble homes using manual indigenous tools. The yarn they spin is later handwoven into fabric by weavers in the same area.
In essence, khadi is a fabric made with handspun yarn which is handwoven, whereas handloom fabric uses mill-spun yarn. What makes patnulu khadi special is that the entire process of growing the native cotton crop to making the yarn and then the fabric is done by hand by spinners living within a radius of a few kilometres. This preserves the original idea of khadi as a locally self-sufficient production system. Most of the khadi today is made from yarn produced by the ambar charkha, a multi-spindle charkha developed in the second half of the twentieth century. The technology, scale, context and economics of ambar charkha-spun khadi is very different from how patnulu khadi is spun, thus making patnulu yarn and its fabric production a unique case study.
The major patnulu khadi products sold in the market today are plain, undyed fabric. Saris and dhotis with small motifs and temple borders are also woven for designers and niche markets, mostly on made-to-order basis. The AFKK’s own retail outlet in Ponduru town keeps a small quantity of patnulu khadi. The legendary Telugu actor Akkineni Nageswara Rao (ANR) was known as a big patron of Ponduru khadi and even has a dhoti, the ANR dhoti, named after him.
Ponduru Khadi and Gandhi
There is not much historical documentation available on Ponduru hand spinning itself. Ponduru came to limelight after Gandhi, during his cross-country travels, visited the town in the 1920s when he came to know about its spinning tradition. Gandhi used to only wear cloth woven from yarn spun by himself; however, impressed by the finesse of the khadi he saw at Ponduru, he is said to have bought some cloth for personal use and sent his son Devdas to the town to understand the practices closely. Gandhi even wrote about Ponduru khadi in Young India.[1]
Khadi was associated with India’s freedom movement after Gandhi gave a call to adopt spinning as an act of defiance against British imperialism, especially in the context of Indian cotton being supplied to feed the British cotton mills. Thus, the spinning wheel or the charkha became a symbol of resistance and self-reliance, and khadi became an expression of India’s fight for independence. Post-Independence, gone was the context of khadi which made it the common person’s cloth. As textile mills with Western technology started using American long-staple hybrids, there was a fall in the production of native short-staple cotton varieties that were suitable for hand spinning.[2] The shift hurt the spinners of traditional yarns such as the patnulu spinners, a jolt from which they still haven’t recovered.
Patnulu Khadi: Its Uniqueness
To understand the uniqueness of patnulu khadi, it is important to understand the technology that makes the khadi of today, the ambar charkha. Ambar charkha is a multi-spindle charkha developed in the 1950s by Ekambaranathan, a disciple of Gandhi. The main objective of the ambar charkha was to increase productivity of the spinner, irrespective of their skill, and to establish a thriving rural industry to eradicate rural poverty.[3] [4]
While the traditional charkha, also called the Gandhi charkha, is a single spindle charkha on which the spinner actually draws and spins the thread from the cotton and gives it the necessary twist, ambar charkha consists up to 12 spindles and incorporates the ring spinning technique used in spinning mills.[5] In ambar charkha, the role of the spinner is limited to turning a crank either manually or with the help of electricity which automatically operates different components of the charkha. (Fig.1)
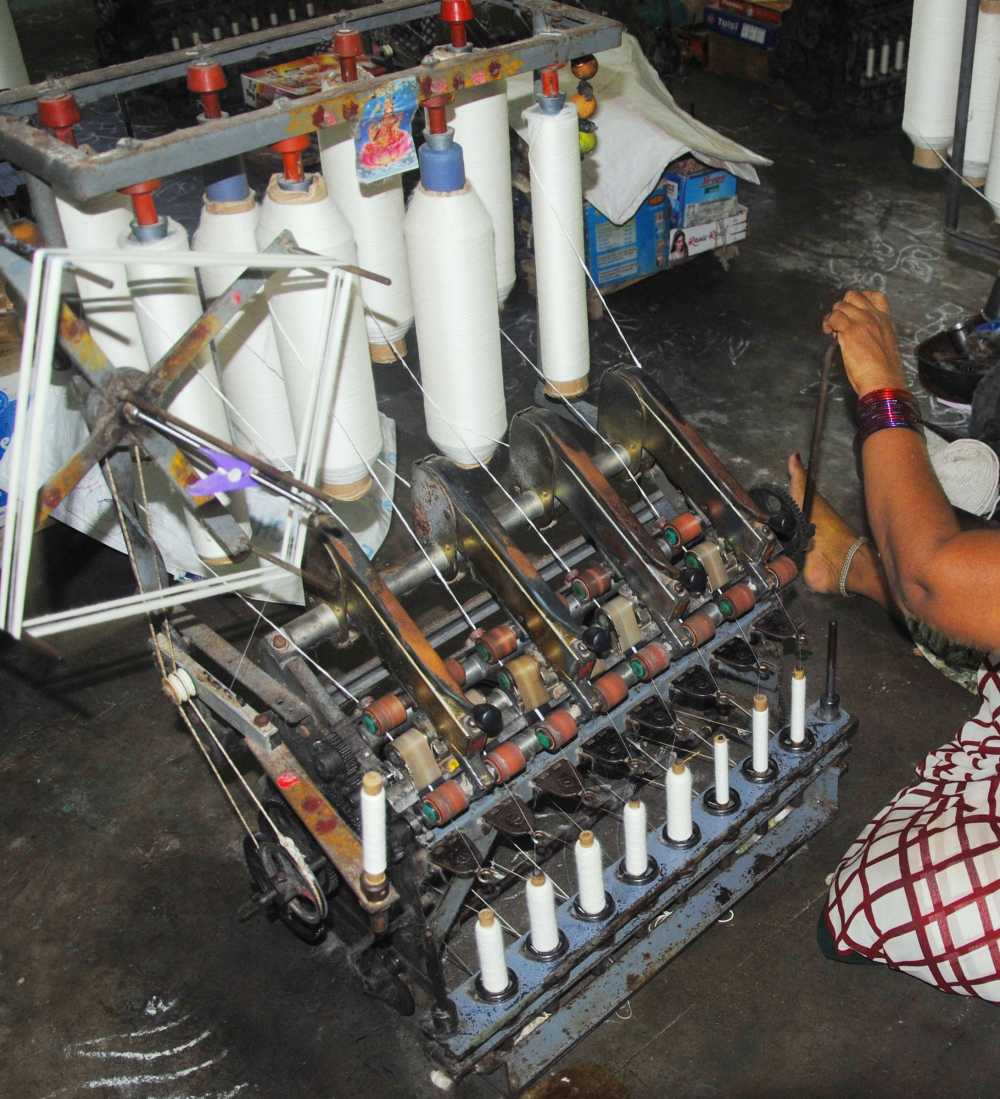
For ambar charkha, the preparatory stages of converting cotton fibre from the pod to a final spinnable form—ginning, blowing, carding, drawing, combing and roving—are all done in centralised and mechanised units run by the Khadi and Village Industries Commission (KVIC). Finally, this cotton is used by spinners to spin yarn on the ambar charkhas, often in khadi units set up by the KVIC. In contrast, for patnulu khadi, the cotton is grown locally, prepared for spinning by the women themselves at home, and spun on the Gandhi charkha.
Though since the 1950s many spinners have shifted to ambar charkha for easier and quicker production and most khadi available today are made in handlooms, patnulu khadi has also survived. Today, according to local sources, there are about 300 spinners and about 350 weavers making patnulu in Srikakulam and the neighbouring district of Vizianagaram. Among these, only about 50 spinners and 15 weavers live in Ponduru town. The spinners belong predominantly to the Pattusali caste though a few other castes also spin. Traditionally, some households might have done both spinning and weaving, but today the spinners and weavers are distinct and do not know each other’s craft. The weavers belong to Pattusali, Devanga and the Sali castes and, usually, both the men and women weave.
Patnulu Spinning: The Process
Raw material
Two indigenous varieties of short-staple cotton, konda patti (hill cotton) and yerra patti (red cotton, due to its pale cream colour) are grown in the area and are used exclusively for patnulu spinning. Conventional BT cotton and other hybrids cannot be used in patnulu spinning; spinners are supplied cotton from the khadi sangams (cooperative societies) they are affiliated with and in some cases buy directly from the farmers. These perennial cottons are rainfed and organic, but nowadays some farmers use a minimal dose of fertiliser and irrigation to improve yields. Konda patti is used for spinning finer yarn counts of 71 to 100, whereas the yerra patti is used for coarser counts, 44 to 65. (Fig. 2)
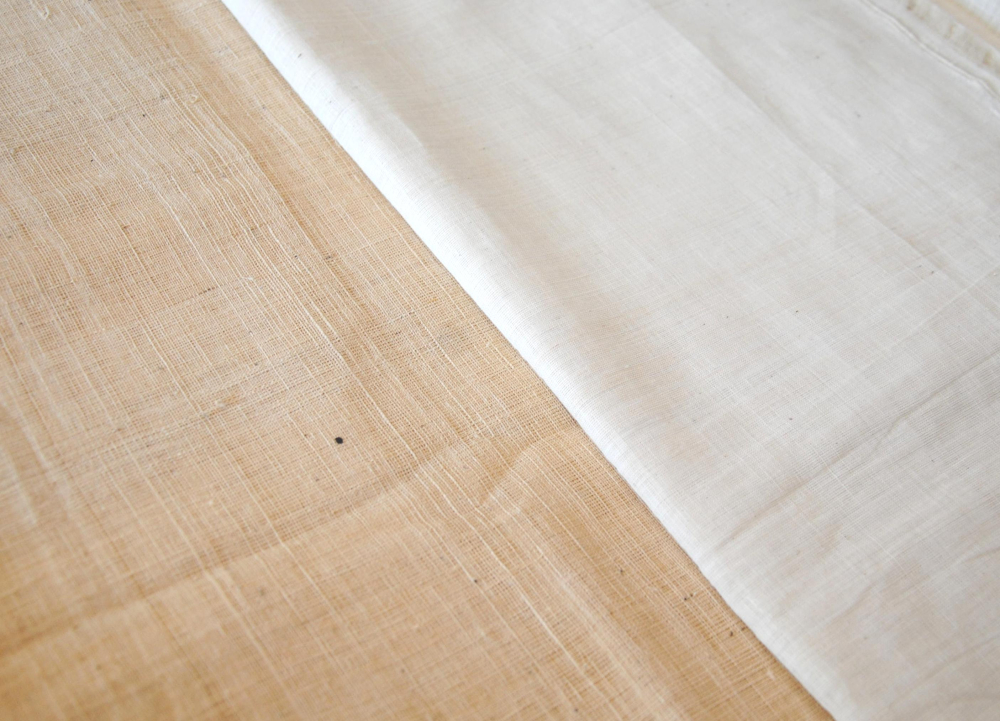
Ginning
Ginning is the process of cleaning the cotton of impurities like dried leaves, soil, etc., and separating the seed and the fibre. First, the cotton with the seed is repeatedly combed with a fish jawbone (of the wallago attu, locally known as valuga) to remove the minute impurities and straighten the fibres around the seed. (Fig.3)
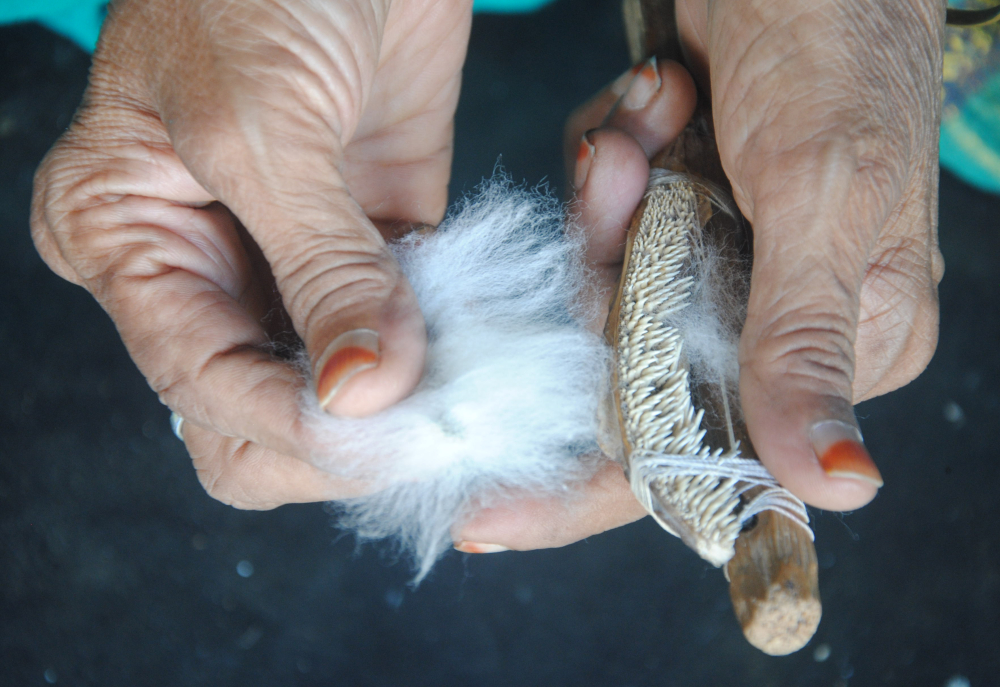
To separate the seed from the fibre, each pod is laid on a wooden plank and rolled using an iron rolling pin in the manner of rolling chapattis. Some spinners also use a hand-operated wooden gin which consists of two closely set wooden rollers that separate the seed from the fibre as the cotton passes between the rollers. Although using a wooden gin is faster than the rolling pin method, both the processes are in use.
Drawing and straightening
The ginned cotton is passed multiple times through the balni (local name for a double-drum roller) to straighten and draw out the fibres. The result is a loose, mass of fibre that looks like combed cotton and increases in length every time it is passed through the rollers.
Carding
Carding eliminates final traces of impurities from the opened fibres, and separates the tufts, lumps, and immature fibres.[6] In hand spinning, carding is done using the carding bow. The straightened fibres from the balni are placed on a wooden plank and the spinner continuously plucks the carding bowstring and applies vibrations to the loose mass of cotton to open up the fibre. (Fig. 4)
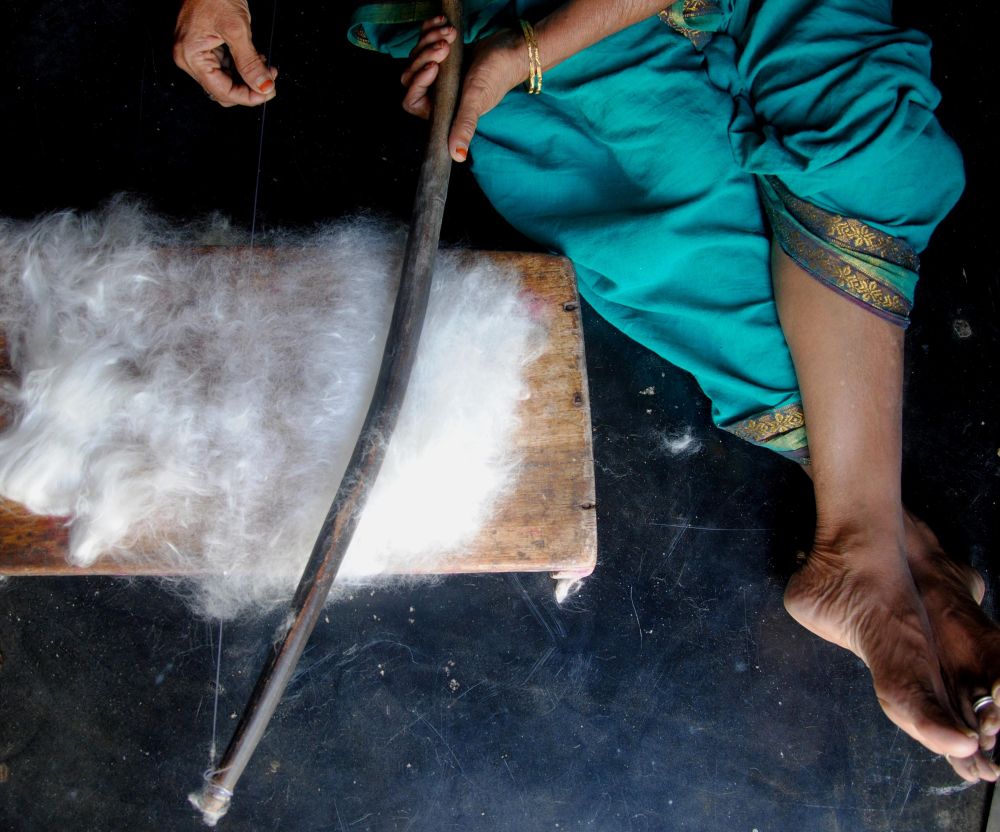
Sliver rolling
The airy mass of fibre is loosely rolled into a sliver using a wooden stick. The cotton is ready for spinning and is kept stored in palm leaf boxes.
Spinning
When the spinner is ready to spin, the cotton sliver is held within a piece of dried banana stem. As the spinner turns the wheels of the charkha with her right hand, she simultaneously draws and twists the cotton with her left hand to make yarn and winds it on to the spindle. Drawing the yarn out evenly and giving it just the right twist is a test of the skill of the spinner. (Fig.5)
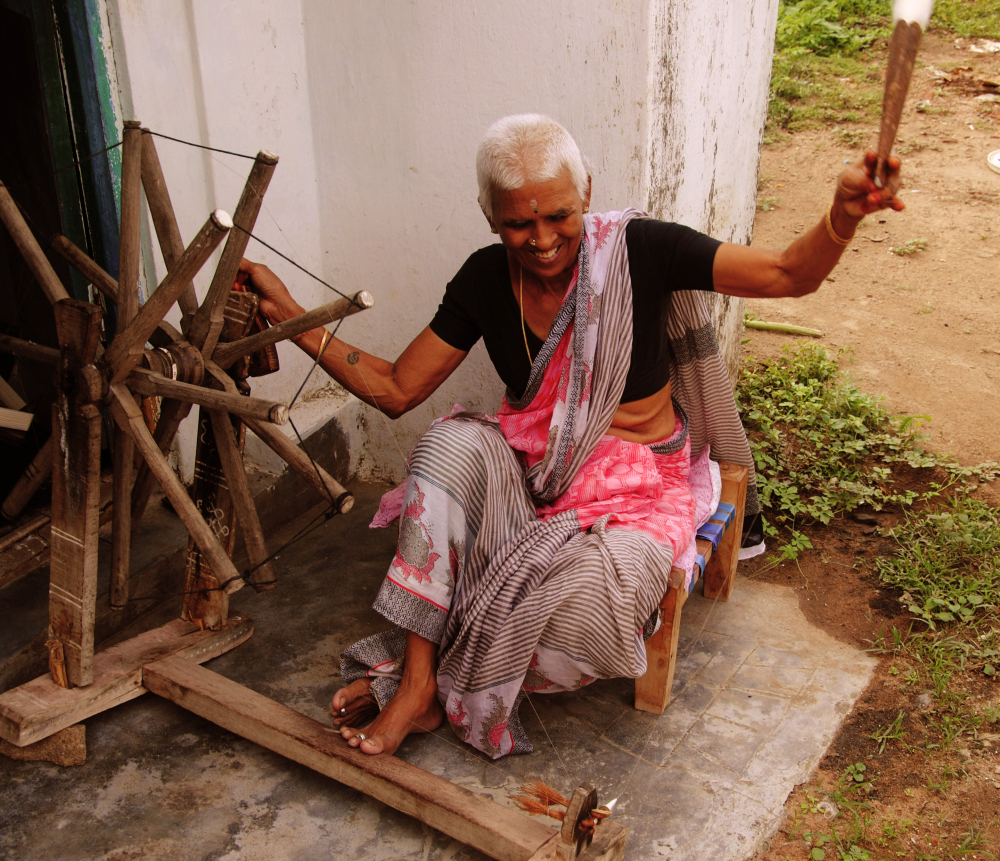
Hank making
The spun yarn is made into hanks for weaving. A hank is a circularly wound yarn which is usually 1,000 metres. The spun yarn on the spindle is reeled off and wound around a rotating frame. After every 1,000 metre, the circularly wound yarn, now a hank, is removed off the frame, tightly twisted and stored. At times, some spinners also dye the hank before weaving. (Fig.6)
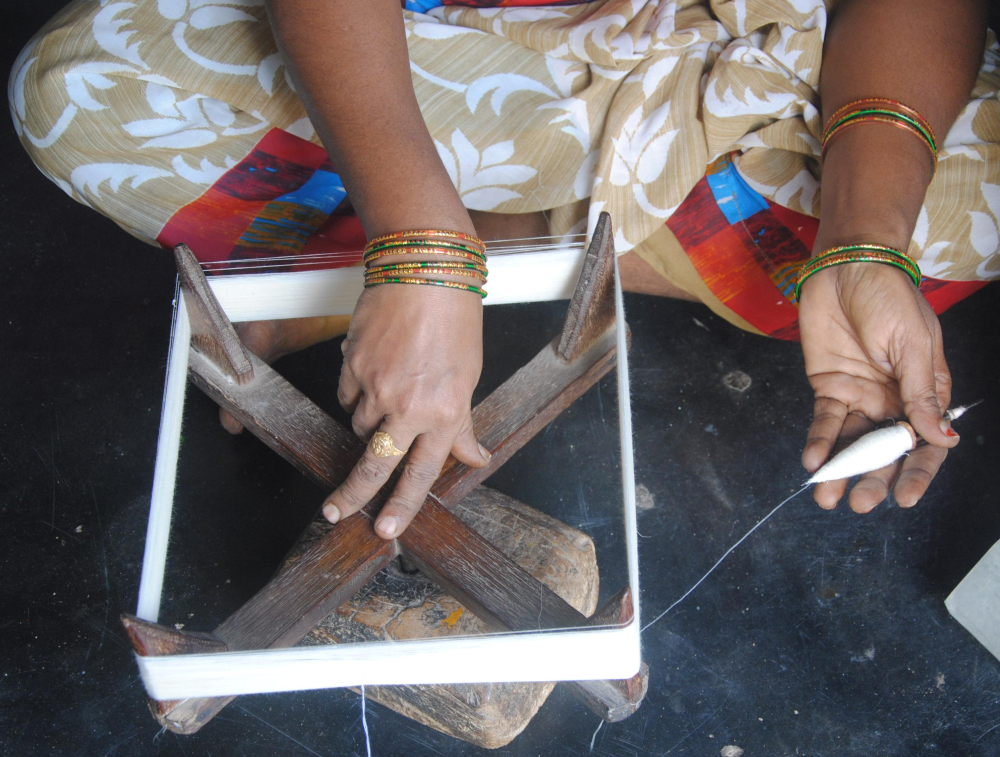
Weaving
Though the steps in patnulu weaving are similar to general handloom weaving, it requires extra care and effort. Patnulu weaving consists of the following stages:
- Bobbin winding: The hank yarn is mounted on a revolving bamboo frame and is wound on to cylindrical bobbins using a winding charkha.
- Preparing the warp: Multiple bobbins are then used to prepare the length and width of the warp by winding it on an aasu (a large wheel).
Street sizing
Unlike conventional khadi yarn which may be hank sized in other parts of India, patnulu yarn is street sized, meaning the yarn is actually spread out on the street and sized. Sizing is the process of applying diluted rice gruel on the yarn and brushing it multiple times with a special brush made from the roots of the plant that is used for traditional brooms. Street sizing is the most important process in weaving as it adds strength to the yarn and makes it fit for weaving. While street sizing of mill-spun takes about two to three hours, handspun yarn takes four to six hours on good days.
Drafting: To make the yarn ready for weaving, the sized yarn is wound on a beam and drafted through different parts of the loom to make the required width of the fabric.
Weft preparation: In the process of waft preparation, the hanks are wound around pirns (spindle-shaped small bobbins) to be inserted into shuttles for weaving.
Weaving: Finally, as the weaver operates the loom, the warp and weft interlace to form patnulu fabric. Weaving patnulu requires a lot more care than ambar spun yarn due to the uneven, low-twist nature of the yarn. The patnulu fabric is more porous, absorbent, and livelier in texture.
Economics of Patnulu Making
Patnulu spinning is done exclusively by women, mostly old and middle aged. It is important to note that it is practised today as an additional source of income for the family. Spinners lament that their wages do not reward the hard work involved, but they continue because spinning is an occupation they can continue without stepping out of their homes, irrespective of their age. As in many other traditional crafts, there are no takers among the young generation who are all educated and look for jobs in nearby towns. Patnulu spinners spin different counts (denotes the fineness of yarn), from coarser 44 count to finest 100 count. The spinners say that it is the 100s count that is the most remunerative because they are paid a higher price per hank for finer counts; it takes the same amount of time and effort preparing the cotton during the pre-spinning stages for any count.
Weaving patnulu requires extra care and effort compared to ambar khadi. Though probably entire Ponduru and villages around once wove handspun fabrics, now weavers have shifted to either weaving mill spun or ambar khadi varieties since the wages are not in sync with the extra work and attention that patnulu demands. While a 33-metre long warp of conventional mill-spun fabric takes less than a week to weave, patnulu warp may take up to three weeks and ambar khadi weaving falls somewhere in between. (Fig. 7)
To understand the broad economics, let us take the case of 100s count patnulu. For the finest 100s count, spinners are paid between INR 100 to 112 per hank, i.e., 1,000 metre yarn. A spinner can spin approximately one hank per day provided she works for six to eight hours. A weaver needs approximately 300 hanks for a 33-metre long warp, and he weaves one or 1.5 warps per month with his wife’s support. The wages paid for weaving a warp is approximately INR 10,000 from which the weaver himself must pay for different pre-loom services. Thus, a weaver’s loom has to be supported by 10–15 spinners. A very basic costing exercise puts the cost of a 100s count patnulu plain undyed fabric at approximately INR 1,300–1,400 per metre.
Once the fabric is ready, majority of the patnulu spinners and weavers supply their products to the Andhra Fine Khadi Karmikabhivruddhi Sangam (AFKK), the khadi cooperative set up in 1949 in Ponduru, affiliated to central government’s Khadi and Village Industries Commission (KVIC). Until recently, two more sangams were producing patnulu khadi. Nowadays, a few master weavers and social enterprises are also involved in small scale production, which they supply to niche markets.
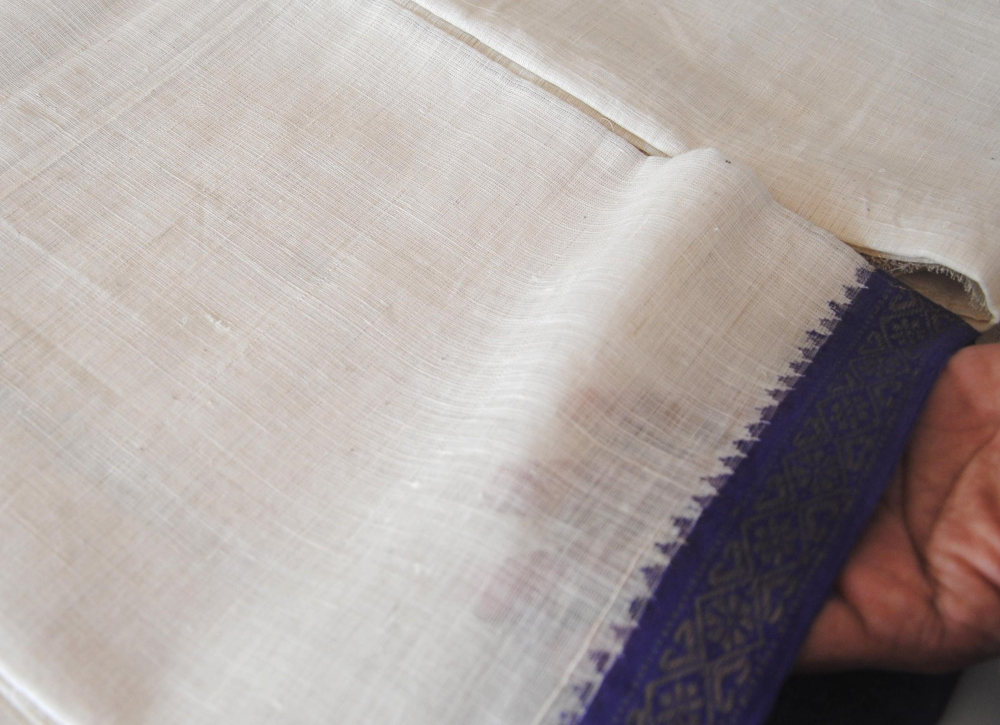
Challenges
Today, Ponduru khadi is a generic term for any handwoven fabric from the area. The distinctions between ambar khadi and patnulu khadi fabric are neither explained by the sellers nor understood by the general public. Add to that the power loom fabrics, often sold as handloom, that have taken over the market because of their low cost of production (anywhere between 30–50 per cent lesser than that of handloom), creating further problems for the patnulu khadi spinners as they struggle for buyers.
While patnulu khadi fabric may appear expensive to the average customer, it is exploitative for its practitioners even at the current wages. Even for the finest (100 count) fabric, the average monthly income is about INR 3,000 for a spinner and INR 15,000 for weaving, which includes the weaver family and all the pre-loom service providers.
The craft practitioners lament that the government is not doing enough to bring respect and money to the craft. The number of patnulu weavers and spinners is dwindling and one cannot do without the other. Weaving is a community craft as the weaver is often supported by others like warp makers, sizers, and winders. The spinners also express concern that when their tools develop wear and tear problems, there is no easily available expertise to repair them or purchase new ones. Any missing or weak link in the value chain puts the entire craft at risk. The spinners are the worst affected since the weavers have the choice of shifting to other kinds of yarn; however, if there are no patnulu weavers, the spinners may have to give up their craft entirely.
Conclusion
Patnulu khadi of Ponduru has a special place in the textile heritage of our country for its unique processing and spinning of raw cotton and weaving of fine khadi. However, like many other traditional crafts in India, it is struggling for recognition and to reposition itself in today’s world of digital information and media.
First and foremost, informative and correct labelling of different categories of khadi and handloom is required so that customers can make an informed choice. The need of the day is to implement compulsory labelling for powerloom and penalties for powerloom manufacturers who sell their products as handloom.
The challenge is to ensure that there is dignity, pride, and a decent livelihood for the practitioners of this craft that is not tied entirely to the market economics of the product. This is a challenge for the government and the society at large including patrons of handloom. Innovative textile heritage tours and workshops could be conducted to increase public awareness. The craft itself needs to present itself in a new light to the world as it is an extremely valuable textile heritage which was once India’s pride.
Notes
[1] Shah, ‘Ponduru.
[4] Buch, Puratan. Ambar Charkha.
[5] Jain, ‘Hand-spun and Hand-woven.’
[6] Ibid.
Bibliography
Buch, Puratan. Ambar Charkha. Bombay: Akhil Hind Ambar Seva Sangh, 1955. Accessed January 20, 2020. https://www.gandhiheritageportal.org/ghp_booksection_detail/MzQ3LTg1OC0z#page/1/mode/2up
Dandekar, V.M. ‘Rationale of the Ambar Charkha’. Economic and Political Weekly (EPW) 9, no. 26–27–28 (1957: 863–868. Accessed January 20, 2020. https://www.epw.in/system/files/pdf/1957_9/26-27-28/rationale_of_the_ambar_charkha.pdf
Jain, Rahul. ‘Hand-spun and Hand-woven: Cotton Khadi in the New Millenium’. In Khadi: The Fabric of Freedom, edited by Martand Singh, 28–55. New Delhi: Roli Books, 2002.
Menon, Meena, and Uzramma. A Frayed History: The Journey of Cotton in India. New Delhi: Oxford University Press, 2017.
Shah, Amita. ‘Ponduru: The Life Charkha.’ Open Magazine, ‘The Freedom Issue 2019’, August 6, 2019. Accessed January 20, 2020. https://openthemagazine.com/features/history/ponduru-the-life-charkha/